
「倉庫作業の生産性を上げたいけど、どんな方法があり、何をしてよいか具体的にわからない」
「そもそも手作業が多すぎて、どこから自動化してよいか判断がつかない」
このようなお悩みはありませんか?
昨今の物流に関する規制や、労働人員不足などにより、倉庫内作業の自動化が必須になっています。しかし、急に自動化と言われても、具体的には何をしたらよいかわからないものです。これらはある程度ITや設備の知見が必要となりますので、実際に自動化が進まず困っている方も多いのではないかと思います。
この記事は、長年部品メーカの物流倉庫で管理業務に従事し、マテハンを減らす自動化や、システムを活用したデータインプット作業の自動化を多数実施してきた私が、今後具体的にどのような点に着目し、具体的にどのような自動化を行っていけばよいか解説します。
この記事を読んで頂くことで、今後の自社で行っていく具体的な自動化プロセスを明確に出来ると思います。
それではさっそく見ていきましょう!
倉庫の自動化とは
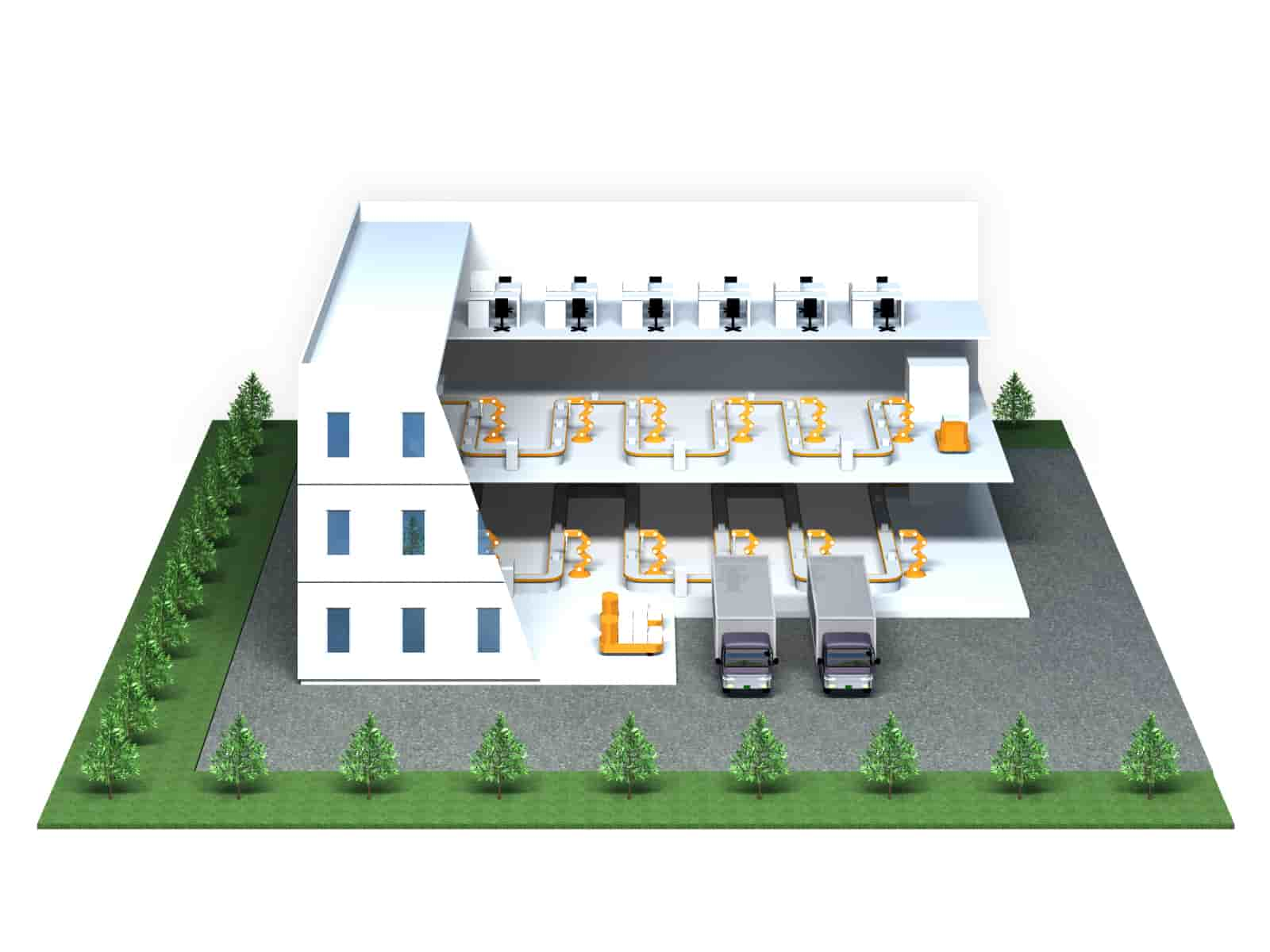
倉庫の自動化とは、人の手を極力減らして倉庫内の作業を効率化する技術やシステムのことです。
具体的には、商品の入出庫、在庫管理、ピッキング作業などが自動化されます。これには、ロボット技術、コンベヤーシステム、ソート機器、自動化された保管および取り出しシステム(AS/RS)などが使用されます。
また、IT技術も重要で、リアルタイムでの在庫追跡やデータ分析を可能にするソフトウェアやセンサーが組み込まれています。自動化により、作業の速度と正確性が向上し、コスト削減や作業員の安全性の向上にも寄与します。
これにより、倉庫は設備やシステムによる自動運営が可能になり、より効率的な物流が実現します。
倉庫を自動化することによるメリット
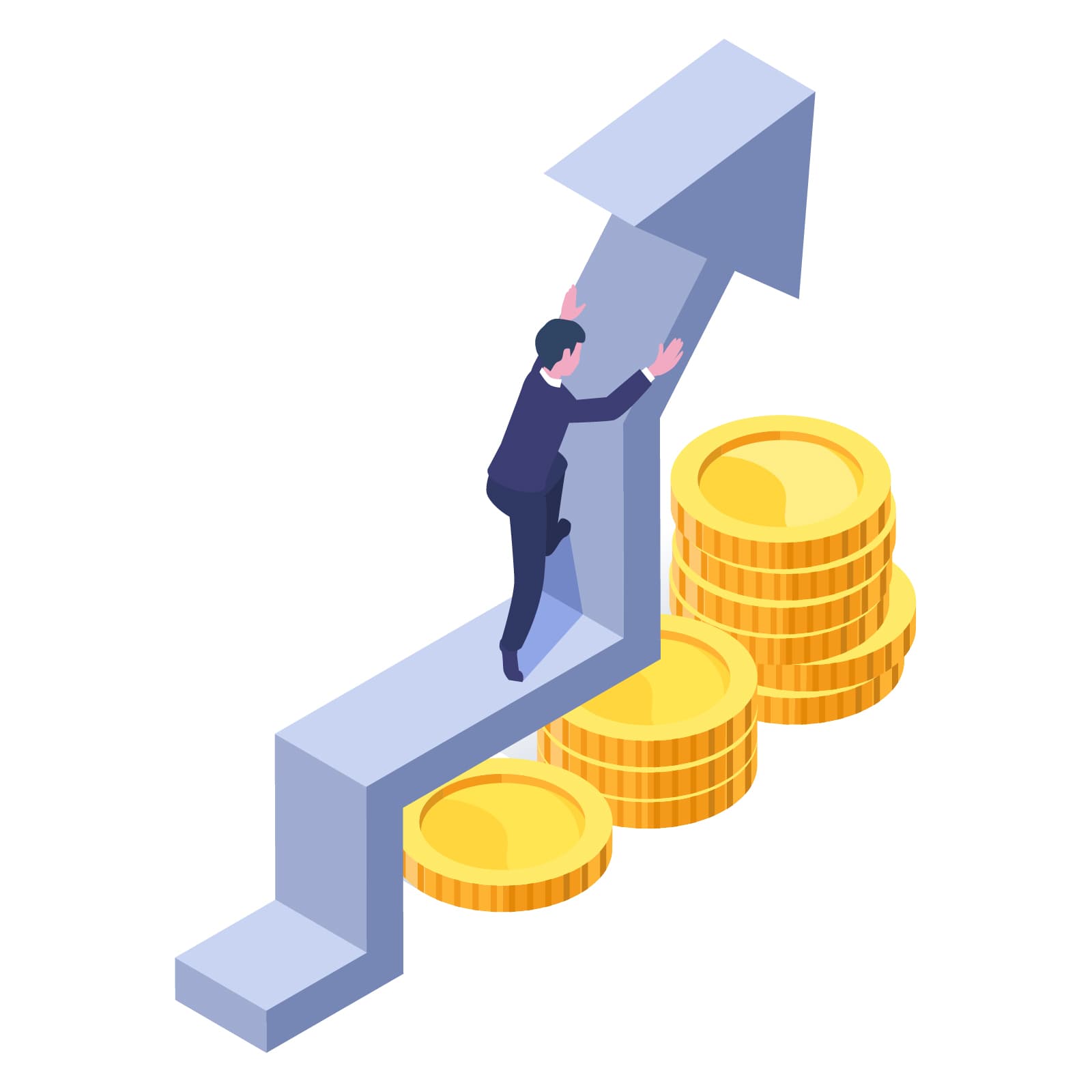
ランニングコストが大幅に削減できる
倉庫を運営するには、倉庫の借料・光熱費・人件費と様々かかります。その中でも、特に人件費は高い割合を占めており、人の作業を自動化することにより、大幅に利益率を向上させることができます。また、これまで人を管理していた管理職やライン管理をするリーダーなどの間接人員も、管理範囲が少なくなる為、間接的な人員も削減することに繋がります。
サービスの質・正確性が向上する
人がピッキングや検品作業などを行うと、必ずどこかでヒューマンエラーが発生します。どれだけ経験が長い人でも、少しのミスはいつか出てしまうものです。自動化設備を利用することで、作業によっては正確性が向上します。検品を自動化すれば人が見落とす箇所も正確に発見します。結果的に、顧客へのサービスの質向上することに繋がります。
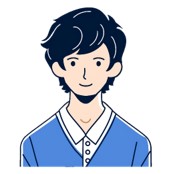
ヒューマンエラーの対処も必要がなくなると考えると、こちらも仕事を減らしている事になりますので、人件費の削減につながっていきますね。
倉庫を自動化することによるデメリット
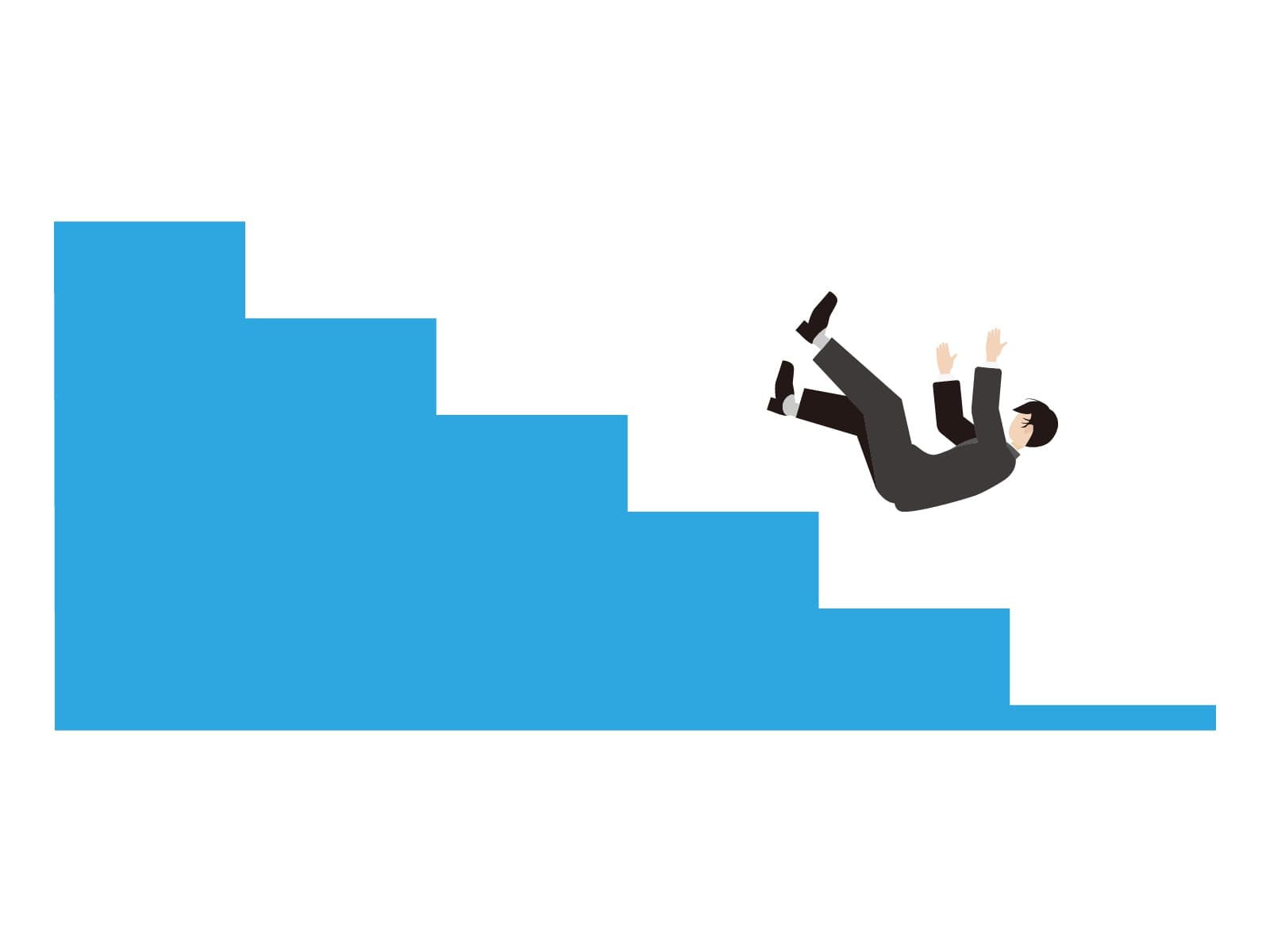
初期導入コストが高い
自動化にあたり、設備でもシステムでも、何を導入するにしても高額になります。
採算性が高く、後で投資効果として回収できる場合であっても、最初に多額のキャッシュが必要になります。これらの調達・準備が一つのデメリットです。資金調達にも労力がかかりますので、これらを踏まえても投資したほうがよいと判断できる場合に自動化を進めていくのがよいでしょう。
専門的な知識が必要
設備やシステムは、専門の開発担当者が必要になります。当然、発注先の担当者と連携を取り、詳細な仕様を決めて導入することになりますので、管理職や経営者が詳しい知識を持っておく必要はありません。
ただ、最低限のリテラシーが無いと、物理的にどんな開発が可能なのかなどが分からず、相手が言うまま開発を進めてしまい、結局思っていた設備にならなかったというケースも少なくありません。
全く設備やITに関する知見が無い場合は、ある程度事前に学習したり知識を高めておく必要がありますので、これらがデメリットといえます。
どの工程を自動化するのか
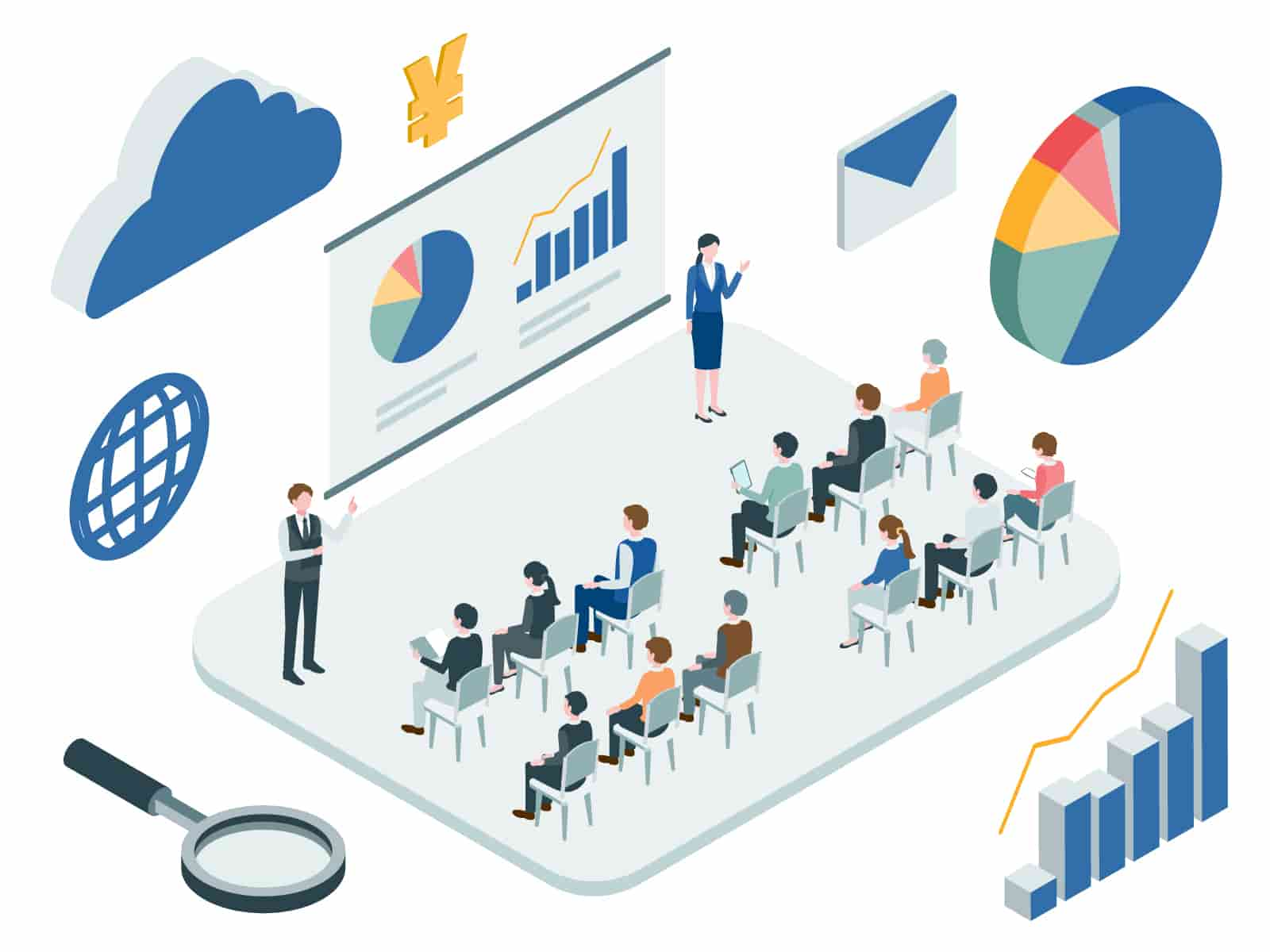
まず、倉庫を自動化する上で大切なのは、「どこを自動化するか」を間違えない事です。
設備にせよシステムにせよ、導入には高額な初期投資が必要です。つまり、中長期で投資回収できるかどうかを明確にしておかないと、無意味な投資となってしまいます。
結果的に、人がやっていたほうがよかったとなってしまっては、元も子もありませんので、これらは事前にしっかりと自社の状況と照らし合わせて判断しましょう。
基本的な判断軸は2つです。
人員がたくさん必要な工程
1つ目は、単純に人員数が多い工程です。それだけマテハンが多いということになりますので、自動化により得られる効果が大きい可能性が高いということになります。
また、人員の多さは、管理者や庶務といった、間接的な人員の多さも判断目安の一つになります。理由はさまざまあると思いますが、人員の多さは、直接作業をする人が多い場合と、直接作業はしないけど、間接的に関係のある仕事をする人が多い場合の2種類あります。後者の場合であっても、自動化するポイントによっては、間接的に発生する作業を削減することが出来ます。
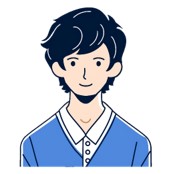
間接的な作業をする人が多い場合は、システム系の自動化を進めたほうがよいパターンが多いです。
離職が激しい工程(難しい・きついなど)
2つ目は、離職が多い工程です。難しい・きついなど、何らかの理由で、特定の工程のみ人材が安定しない場合があります。このような工程も自動化することで、採用コストや、日々の管理コスト(教育・日常管理など)において大幅な削減が見込めます。
離職量や率を管理指標としてベンチマークしていない場合は、一度過去の状態を調べてみるといいと思います。思った以上に人が定着していない工程や、採用コストがかかってしまっている場合があります。
設備を検討する際に考えるべきポイント
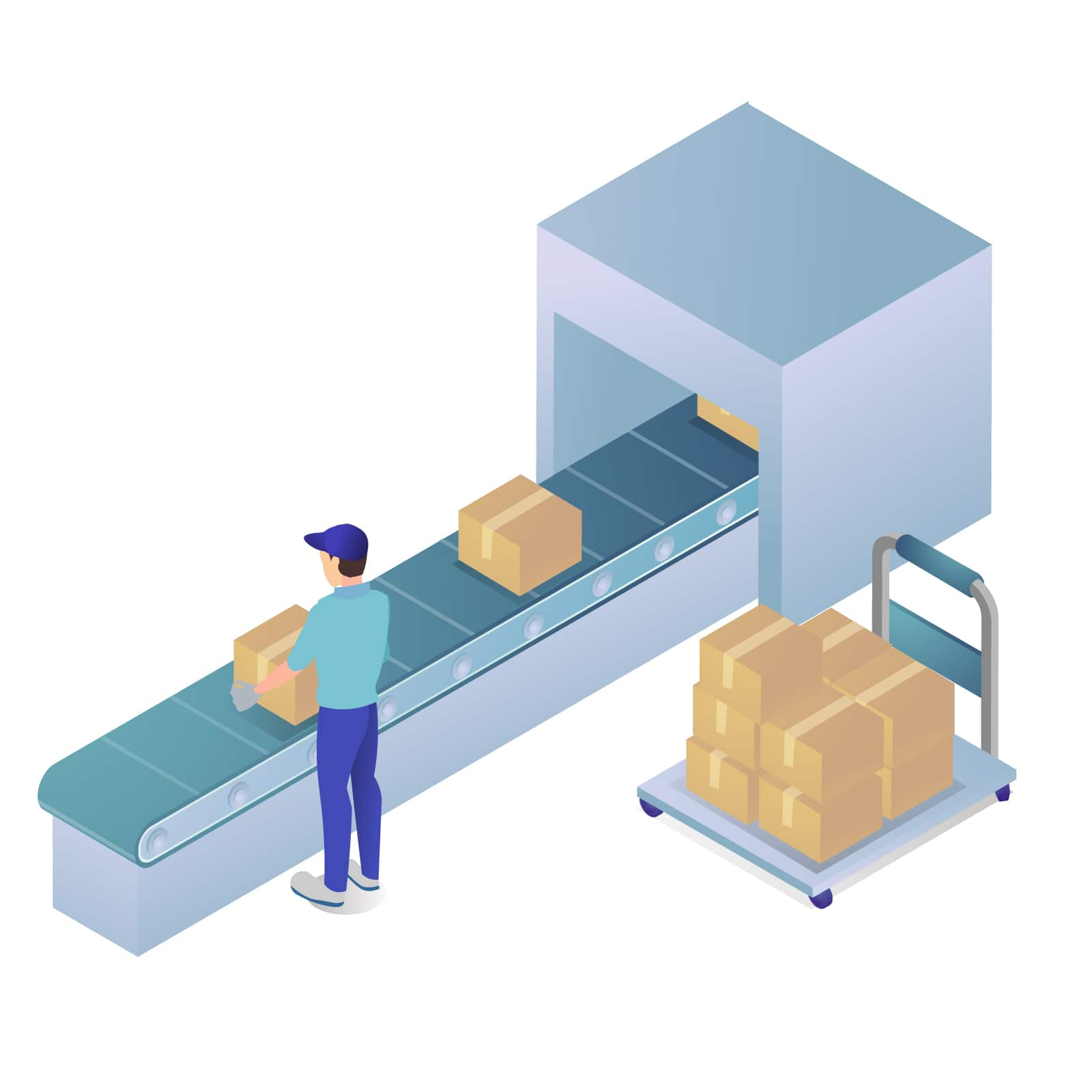
どこに、どのような設備を導入するか決まったら、次は設備の仕様をどのようにするか明確にしておくことが大切になります。ここでは、具体的にどのような観点で設備仕様を決定していくべきかポイントを解説します。
投資回収が最低でも5年以内に完了するか
高額な設備投資となる場合は、固定資産扱いとなり、基本5年で償却(経費計上)を行います。つまり、5年以内に投資回収できない場合は、効率が悪い投資といえます。高額な投資をする場合でも、5年を目安に回収できるかは試算しておきましょう。
長期的に利用できるか(長期ニーズ+耐用年数)
例えば、シンプルな構造の設備であれば、5年の経費計上が完了した後も、メンテナンスにより長い期間利用し続けられる設備もあります。このような設備は、利益に寄与する割合が大きい設備といえます。設備を導入する際には、その設備がだいたい何年くらい利用可能で、メンテナンス負担の有無などを考慮しておくとよいでしょう。
また、もう一つ考えておかなければならないのは、長期的にその設備が有用かどうかという点です。もし仮に10年耐用できる設備であっても、10年後には周辺の運用や顧客が変わったなどの理由で、使えなくなる可能性があります。
つまり、設備を導入する際は、必ず普遍的に利用できそうなポイントから固めていくのがよいということになります。
仕様変動の有無
これらは設備でもシステムでも言えることですが、例えば自動倉庫を導入したとして、倉庫に入れる商品の外寸が大きく変わったため利用できなくなった などというケースもあり得ます。システムも同様に、これまでのインプット条件から、大きく項目や量が変わってしまうといったケースもあります。
このように、開発当時と数年後で取り扱う荷物や情報が変わって利用できなくなったということを防止する為に、これらも普遍的な作業を見極めて、そのポイントで導入することをお勧めします。
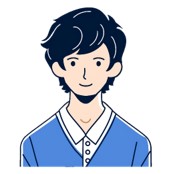
ユーザー側でカスタマイズできる要素も踏まえて設備やシステムを開発しておくのも一つ大切なポイントです。
導入方法(レンタルorリース等)
ここまでは自社で設備購入する事を前提としてガイドしてきましたが、設備はレンタルやリースという手段を取る事も一つです。レンタルであれば、契約期間はあったとしても、自社で買い取っているわけではない為、上記のような仕様変更や必要性の低下リスクに対応しやすいです。
また、リースやレンタルの場合は、併せて保守サービスが契約出来る場合もありますので、導入後の管理に不安がある方にもお勧めです。導入したいポイントを明確にしたら、長期的な運用も踏まえてレンタルか自社開発かを検討するとよいでしょう。
倉庫を自動化する方法
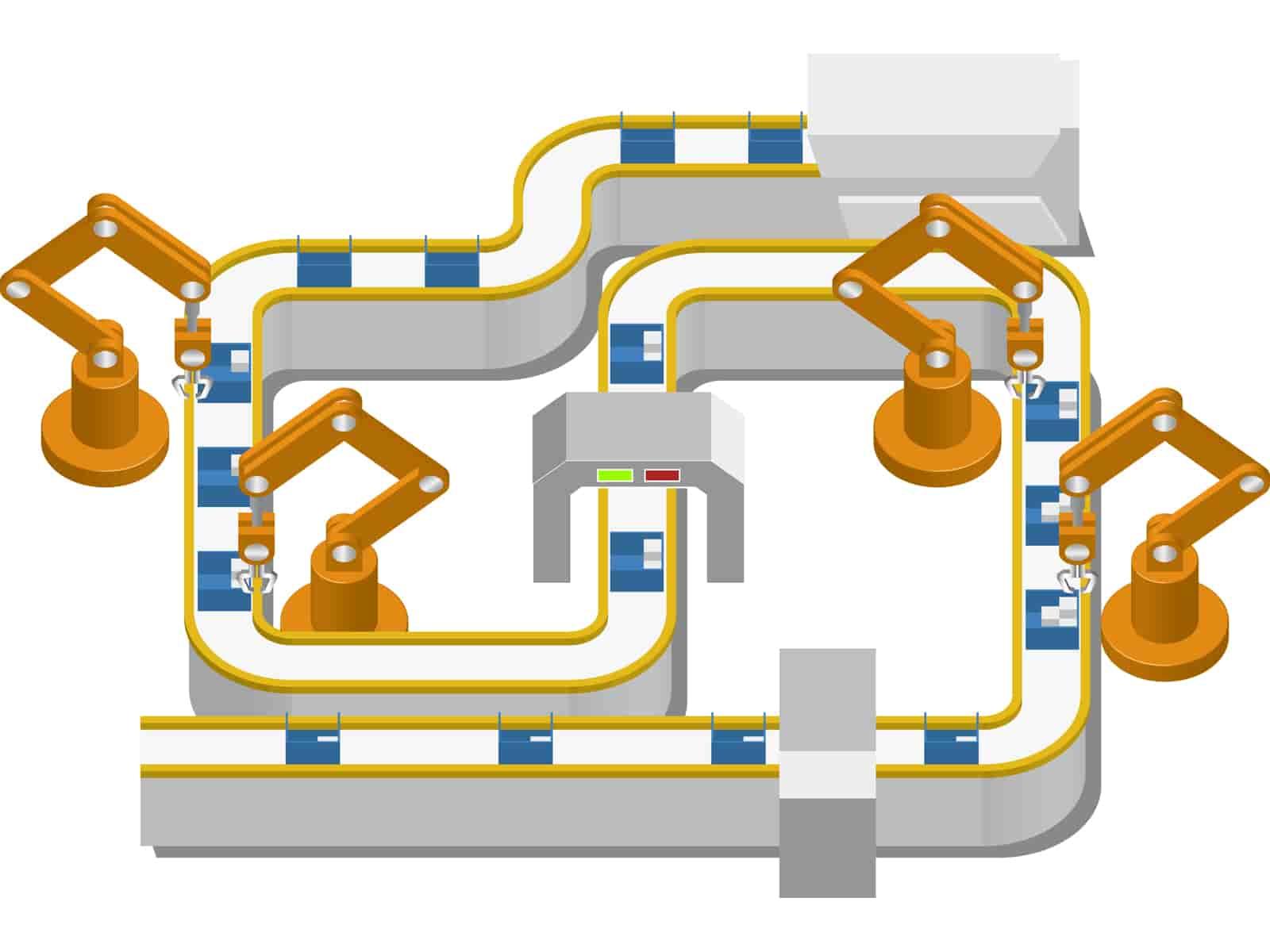
どの工程を自動化するか決めても、具体的にどのような設備やシステムが存在するのか知っていないと導入が出来ません。ここでは、参考になるような設備の一例を紹介します。
自動倉庫
自動倉庫システムは、商品の保管と取り出しを自動化する技術であり、物流の効率化とコスト削減を実現します。このシステムでは、高い位置までの収納が可能であり、空間の最大化を図れるため、限られた敷地内で最大限の収納能力を確保できます。また、ロボット技術による精確な商品の位置決めが、人手による作業よりも速く、正確に行えるため、時間とリソースの節約に貢献します。
自動搬送機
自動搬送機(AGV:Automated Guided Vehicles)は、製品や資材を倉庫内の指定された位置から別の位置へ自動で運ぶ装置です。これらはプログラムされたルートに沿って動作し、センサーやカメラを用いて障害物を回避しながら効率的に動作します。AGVは、特に繰り返し行われる物品の移動において、作業の自動化と時間短縮に非常に効果的です。
自動搬送コンベア
自動搬送コンベアは、製品や資材を倉庫内の所定の位置へと効率的に移動させるために設計されています。これらのコンベアシステムは、自動化されたセンサー技術を利用して、物流の流れを最適化し、製品の搬送と分類を迅速かつ正確に行います。耐久性と高い運転効率を備えており、連続稼働にも対応できるため、生産ラインの効率向上と運用コストの削減に大きく貢献します。特に、多品種少量生産が求められる現代の製造業において、柔軟かつ迅速な物流対応が可能となります。
自動ピッキングシステム
自動ピッキングシステムは、注文に基づいて商品を自動的に選び出し、梱包ラインへ供給するシステムです。この技術により、人手によるピッキングの誤りを削減し、出荷の正確性を向上させます。さらに、作業の速度も上がるため、顧客への迅速な商品提供が可能となり、顧客満足度の向上にも寄与します。
在庫管理システム
在庫管理システムは、倉庫内の商品の在庫状況をリアルタイムで把握し、最適な在庫レベルの維持を支援します。このシステムは、購入、保管、出荷の各プロセスにおけるデータを一元管理し、過剰在庫や品切れのリスクを最小限に抑えます。また、データ分析機能を用いて在庫の動向を予測し、より効率的な在庫管理を実現します。
自動検品(画像検査機など)
自動検品システムは、カメラやセンサーを使用して製品の品質を検査する技術です。画像検査機は、製品の表面の欠陥や異物の有無を高速で精密に検出することが可能です。これにより、製品の品質保証が向上し、不良品の出荷リスクを大幅に減少させます。また、作業効率の改善により、全体的な生産性の向上に貢献します。
伝票ソーター
事務所で発行した伝票類をセットすると、あらかじめ決めておいた規則・情報に基づいて伝票を並べ替えたり、仕分けする装置のことです。小口ロットの注文が多い、同じ伝票発行システムで、大量の配送先に分けなければならないなど、事務処理に人員を割いている場合の改善には非常に有効です。
倉庫の自動化を進めるにあたり実施しておくべきこと
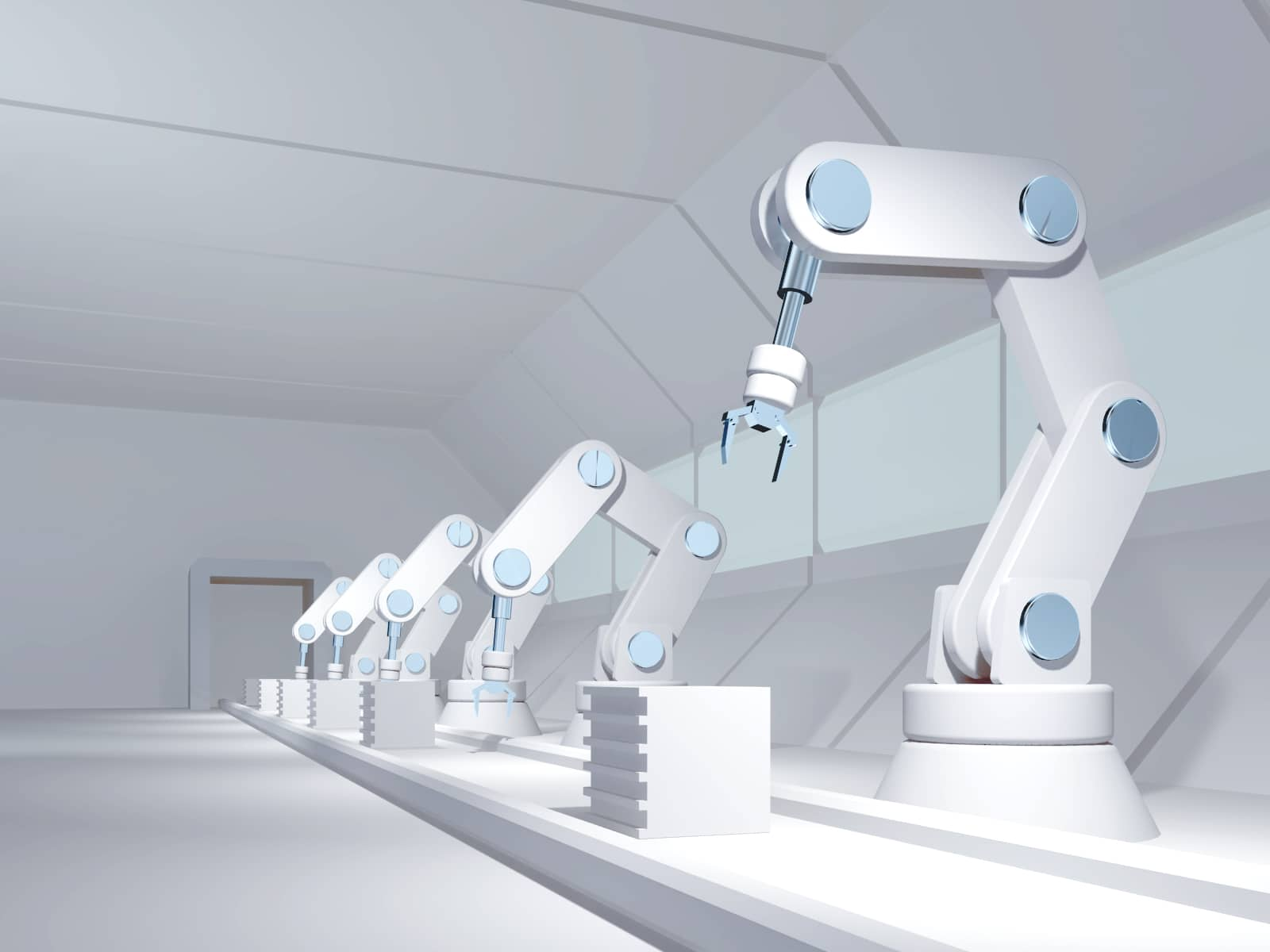
最後に、自動化する設備やシステムを開発すると同時に進めておいたほうがよいことを紹介します。
社内の保守体制構築
物流倉庫の場合、仮に大きな会社であっても倉庫自体にシステムや設備保守の部署が常駐している可能性が少ないです。つまり、設備やシステムの緊急復帰が必要となった場合にすぐ対応が出来ない状況が発生します。誰も保守ができない体制で利用を続けると、このようなケースが発生し、サービスへの影響が出ますので設備の導入と合わせて保守体制の構築も進めておきましょう。
外部保守サービスの確保
もし社内で保守体制の構築が難しい場合は、保守サービスを検討しましょう。特注で製作した設備やシステムの場合は製作した業者様に相談し、サポートが可能か検討してみましょう。市販されているサービスを利用した場合は、その製作元で保守サポートが行われている場合が多いので問い合わせてみましょう。
緊急時の対応フロー明確化
もし設備が停止すると、どの程度完成品が存在しており、何時間後まで顧客生産に影響が出ないかなど、停止すると具体的にどのような状況になり、何をしなければならないのか明確にしておきましょう。あらかじめこれらが把握できていれば、設備の復旧にいつまで時間をかけてもよいか、お客様へも影響が出るのであれば、どのような対応をしておけばよいかなど、緊急時にもスムーズに対応ができます。
まとめ
いかがでしたでしょうか。
設備やシステムを導入することにより、大幅なコストダウンを狙える一方で、どこにどれくらい投資し、導入後の管理体制を整えるなど、戦略的に進めていく必要もあります。
記事の内容を参考にし、自社に合う設備導入を検討してみてください。